Company
Certex Swe
What We Did
Assembling Wind Turbines
CERTEX Engineers Assembles Groundbreaking 105-Meter Wooden Wind Turbine Tower
CERTEX Sweden received an exciting request from the wood technology company Modvion: to assemble and lift sections for a 105-meter-high wooden wind turbine tower—currently the tallest in the world. Adam Johansson, the construction manager and project leader, talks about a project where the Special Products team in Varberg created a unique lifting solution.
Wind turbines are usually made of steel or concrete, but as part of the green transition, Modvion is investing in groundbreaking technology where towers are built from sections of molded wood, which can reduce carbon emissions by at least 25 percent during manufacturing. The wood's lower weight and the modular concept mean that towers can be built taller and transported on public roads. Moreover, laminated wood is stronger per unit weight than steel.
Lifting and erecting the 14.6-meter-long and 11.5-ton sections on-site requires experts of the right caliber. In other words: a perfect job for the CERTEX team in Varberg, where high competence and extensive experience in designing specialized lifting beams and tools are a hallmark.
"Innovation and finding smart solutions is our strength. Additionally, we have a thorough understanding of guidelines, regulations, and directives, which ensures that we always deliver products that are both tailored for the specific customer needs and compliant with all relevant laws and safety requirements," says Adam Johansson.
Custom-made Cradle
A specific requirement from the client, Modvion, was that no marks could be made on the sections, therefore extensive calculations were needed to ensure good safety margins in relation to maximum surface pressure. To succeed with the project, two central components were designed—a "cradle" and a specially manufactured lifting tool.
The function of the cradle was to align the sections at the correct angle before lifting, and it was designed to match both the angle and the conical shape and tilt of the sections. The lifting tool was then to be attached and locked to one section at a time with a determined lifting point on the inside. Wood protection was mounted on the tool to match the internal shape of the section. The actual lift was then performed using a mobile crane connected to the lifting tool.
"To protect the sections, we decided to use rubber mats, which also needed to be custom-made. When we were developing these protective pads, we contacted and collaborated with a consultant who is an expert on rubber," explains Adam Johansson.
Load testing with twice the maximum load
Before the wooden sections could be lifted into place, load testing of the lifting tool with specially designed fixtures was conducted at CERTEX's testing facility in Varberg, to ensure the durability of the different load cases the tool would face in reality.
"We physically load test all our lifting tools with twice the maximum load. In this case, it was extensive work and a tricky project—which we of course solved," says Adam Johansson.
The most exciting part of the whole project was the erection of the sections, considering both the shape and material, he says.
"They are large, heavy to lift, and have special shapes. At the same time, they had to be lifted with precision without being damaged, and then glued together. The lifting angle had to be exact; otherwise, it would cause too much strain on the tool."
Through good collaboration and dialogue with Modvion, CERTEX was able to realize their vision. The 105-meter-high wooden tower can now be seen outside Skara. The inauguration took place in early March 2024, and the wind turbine, owned by Varberg Energy, is already operational and producing green electricity.
Watch the story below!
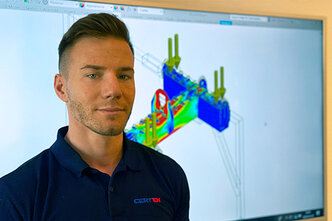
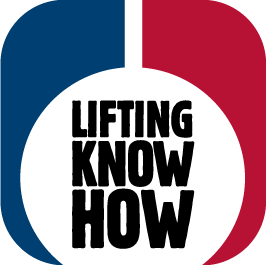